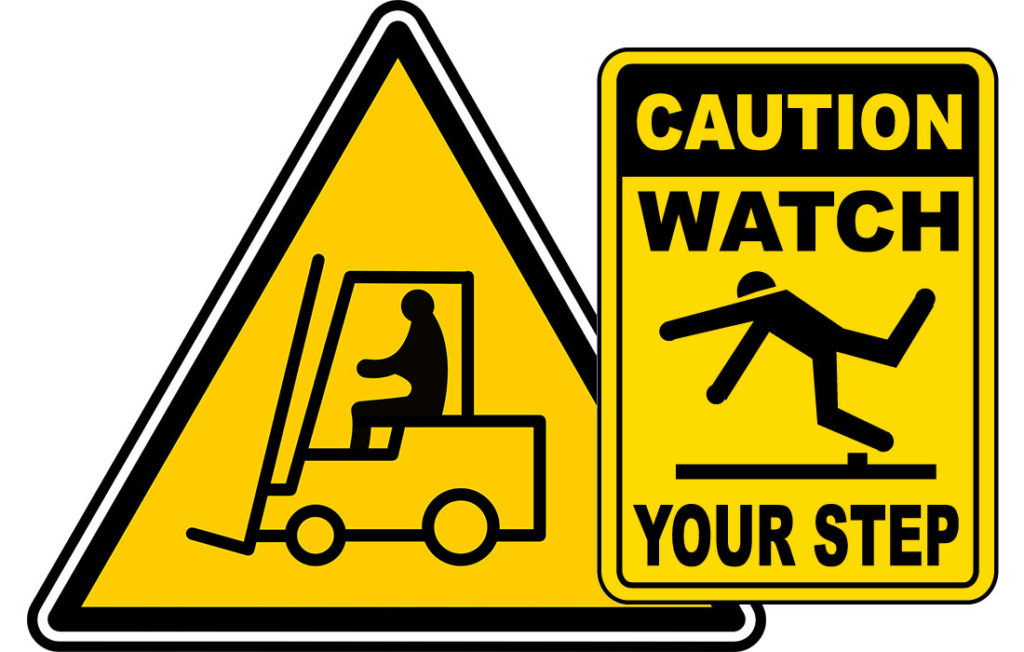
Warehouse Safety Management
Safety in warehouse management can protect the health and lives of employees. Warehouse Supervisors, Health & Safety Officers and all warehouse employees need to work together to reduce risks on a day-to-day basis. By taking the correct precautions and promoting safe working practices, your company can help prevent illness and injury and become a safe and healthy workplace.
There are five main areas of risk to be aware of:
- Slips and Trips
- Manual Handling
- Working at Height
- Vehicles Internal and External of the Warehouse
- Moving or Falling Objects
Slips and Trips
In warehousing and storage, slip and trip incidents can happen anywhere, often they are brushed off as trivial, but most of theses incidents can be avoided.
Tip to Avoid Slips and Trips
Typically, slips happen because the floor is wet or contaminated. In the warehouse environment this could be anything from water, oil, cleaning products or foodstuffs that cause workers to slip.
To prevent this, people need to try and stop the floor getting contaminated by maintaining equipment and cleaning up any spills immediately. In addition, the appropriate warning signs should be displayed when the floor is known to be slippery.
Uneven surfaces or objects on the floor are the usual causes of trips. Items including waste packaging, banded strapping loops and the products themselves are common items that might be left on a warehouse floor as potential trip hazards.
Reducing the risk of tripping in the workplace is largely down to good housekeeping and employees being vigilant by removing obstructions and keeping cables tidied away. If running cables across the floor is unavoidable, you should use heavy-duty cord covers or look to suspend cables at high levels, beware that this may cause an additional hazard to forklifts etc
Manual Handling
As you might expect, the warehouse and storage industry have a higher than average rate of musculoskeletal disorders at 1.9% (per 100,000 workers) compared to 1.2% of workers across all industries.
In 2019/20, a total of 8.9 million working days were lost due to work related musculoskeletal disorders. This equated to an average of 18.4 days lost per case. Manual handling is clearly a high risk task that needs to be properly assessed and managed, especially in a warehouse environment.
Tips to Prevent Manual Handling Accidents
The best way to prevent manual handling accidents is to avoid manual handling altogether. If possible, use alternative solutions such as lift trucks, pallet trucks, trolleys, etc. Operators of lifting equipment need to know the maximum safe working load (SWL) to avoid wearing the equipment down and risking the load falling off.
Despite this, all staff should be trained in safe manual handling to ensure they know their manual handling weight limits (20 – 25kg is heavy for most people) and how to use proper handling techniques to minimise strain.
If manual handling is unavoidable, the risk of injury occurring has to be minimised by carrying out a manual handling assessment. You should consider:
- the task – what needs to be lifted and where is it going?
- the load – how heavy is it? Does the lift need to be completed by multiple people?
- the working environment – are there lots of people of vehicles in the area that need to be considered?
- individual capability – is the load too heavy for that person alone?
- other factors – consider the route, the height of the load and the starting position of the load.
Manual handling includes lifting, lowering, pulling, pushing etc.
Working at Height
In 2019/20, 29 fatal injuries to workers were due to falls from a height, accounting for around a quarter of all worker deaths over the year, a similar proportion to the latest five years combined.
Whether the work is being undertaken by an internal member of staff or a contractor, the work must be risk assessed, properly planned, appropriately supervised and carried out in a safe way.
Tips for Working at Height Safely
Wherever possible, working at height should be avoided because of the risk involved should the activity go wrong. However, if there’s no other way to complete the task, the correct equipment must be used. The equipment itself needs to be inspected periodically, as well as immediately before use and after an incident that could affect its safety.
Similarly, equipment for working at height must be used correctly. This means not climbing on racking or shelving unless it’s specifically designed for use as access equipment.
Alternative access equipment, such as a mobile elevating work platform (MEWP), may require specialist training. Members of staff without the necessary training should not be using these machines. In addition, DIY work platforms created by putting a pallet on a forklift truck is not a safe way of working at height.
Training staff to work at height safely is vitally important. If they have to use a ladder, they should be encouraged to stay off the top three rungs, maintain three points of contact at all times (e.g. two feet and one hand) and use them for no longer than 30 minutes at a time.
Vehicles Internal and External of the Warehouse
Naturally, due to the fact that warehouses are predominantly used to process and house stock before it’s purchased by a customer, there will be a variety of vehicles to be wary of including forklifts, vans and lorries.
All employers involved in the delivery and collection of goods are responsible for the health and safety of their employees as well as any nearby pedestrians that could be affected. Moving vehicles need to be carefully managed to control and reduce the likelihood of accidents.
Tips to Maintain Vehicle Safety in and Around the Warehouse
Legally, only people with a forklift training certification are allowed to operate a forklift truck. In addition, no one under the age of 18 is allowed to drive one either. Therefore, you need to stop anyone that isn’t qualified from operating forklifts.
The design and layout of the warehouse needs to be carefully planned with vehicle safety in mind. Ideally, there will be a one-way system that avoids drivers having to reverse; however, if reversing is unavoidable, you might be able to install mirrors or keep pedestrians out of the area.
Throughout the site, there should be obvious speed limit signs that all drivers need to obey – when driving a forklift, they should not exceed 5mph. A strict zero tolerance policy needs to be enforced for dangerous driving.
Visiting drivers to the warehouse should be given any necessary information in advance to ensure their own safety and the safety of others. You might need to consider how you will communicate site rules with visiting drivers who speak very little English or have a limited understanding of the language.
Where possible, keep vehicles and pedestrians separated. If this is unavoidable, there should be designated walkways with clearly marked boundaries. As well as displaying safety notices and signs for drivers to be aware of pedestrians, people working on the warehouse floor need to be educated to look both ways when they leave an aisle.
Moving or Falling Objects
Being struck by a moving vehicle was the second largest cause of workplace fatality with falling objects being the third largest cause of workplace fatality in the warehouse and storage industry in 2019/20. Preventing these types of injuries is largely focused on stacking items safely and behavioural safety of employees.
Tips to Prevent Objects from Falling
Whether staff are stacking pallets or racking, they need to follow the safe stacking height and weight capacity recommended by the manufacturer. Specifically for pallets, the heavier ones need to be on the bottom and stacked evenly to ensure stability.
Racking systems need to be properly designed and installed which includes being able to safely support the weight of the goods being stored. As previously mentioned, staff should not be climbing on the racking to access higher shelves unless it is designed to be used in that way.
Periodically inspect racking to make sure that it is properly maintained and safe to continue using. In addition, ‘expert’ inspections conducted by a competent and qualified person should also be carried out at specified intervals.
Workers at Risk
Despite working in the same physical space as other people, warehouse operatives can be considered lone workers. Because of the vast space they cover and the layout of most warehouses, employees typically work in isolation from other people.
If we imagine that a worker falls two metres from a ladder and seriously injures themselves, they might not have anyone near them to hear their calls for help. Similarly, a poorly stacked box could fall and strike someone walking underneath, subsequently knocking them unconscious and unable to call for help.